Raku
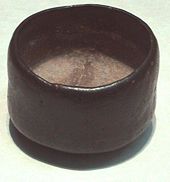
Raku (樂) or Rakuyaki (樂焼き) is a form of Japanese pottery characterized by simple, hand-formed bowls, low firing temperatures resulting in a fairly porous body, lead glazes, and the removal of pottery from the kiln while still glowing hot. Raku is the traditional method for creating bowls for the Japanese Tea ceremony. Raku tea bowls are hand made from earthenware, each with a unique shape, glaze and style.
The Zen philosophy behind the Japanese tea ceremony influenced the artistic style of Raku potters in Japan. For 15 generations, the official Raku title and seal has been used by a line of potters whose work formed the central tea pottery tradition in Japan. Raku was also made by numerous workshops in and around Kyoto, as well as by amateur tea pottery practitioners and professional potters throughout Japan after the publication of a Raku-style manual in the eighteenth century.
Today, Raku is known worldwide as a popular form of ceramic technique, although the Zen philosophy has not been exported with the technique. Many potters in countries other than Japan use this style of ceramic creation—as the kiln need not be large and the results can be exciting—although the technique takes some time to master.
History
The making of Raku ware was initiated during the Momoyama period (1573-1615) by a potter named Sasaki Chojiro (長次郎). Chojiro came under the patronage of the tea master Sen-No-Rikyu (1522-1591), who asked him to create bowls that would match the aesthetics of wabicha, the highly ritualized Japanese green tea ceremony. From that collaboration, Raku ware came into existence.
Chojiro's tea bowls were initially called ima-yaki, literally "now wares," or wares of the "present moment." They were subsequently renamed juraku-yaki, due to the fact that Hideyoshi, the leading warrior-statesman, or Shogun of the time, presented Chojiro's pottery house with a golden seal bearing the Chinese character for Raku. Chojiro's son, also an excellent potter, was awarded the seal, reading "raku" which translates as "pleasure." [1] The term Raku derived from Ju-raku-dai, the name of a palace built by Hideyoshi, one of the great symbols of his age. The family then took the name Raku. This is the only example in the history of Japan of a family name becoming synonymous with the ceramics they produced. Few potter families have continued in an unbroken line in the way the Raku family has done in Japan.[2]
Raku ware marked an important point in the historical development of Japanese ceramics, as it is the first ware to use a seal mark and to focus on close collaboration between potter and patron. Other famous Japanese clay artists of this period include Donyu (1574-1656), Hon'ami Kōetsu (1556-1637) and Ogata Kenzan (1663-1743).
There are several "schools" of Japanese pottery, each of which is focused on a particular region and its unique clay that is found there. There are six main Raku schools, or kilns, in Japan, some dating back to the twelfth century. These schools and their modern-day locations are: • Bizen (Okayama) • Shigaraki (Shiga) • Seto (Aichi) • Echizen (Fukui) • Tamba (Hyogo) • Tokoname (Aichi)
Traditional Raku bowls were usually glazed mostly with black or red colors, yet each ceramic style has its own special look as a result of not only the form, shape of the bowl, and glaze, but also the chemical composition of the clay of the region and the type of wood used to fire the kiln.[3]
Kilns in Japan began in the fifth century when from Korea the Anagama style kiln was imported. It is a single-chamber, wood-burning kiln built on the side of a hill; these are still in use today in many parts of the world. In the seventeenth century, the Noborigama (multi-chamber climbing) kilns were invented, which allowed for greater production during one firing.
Chojiro's style and philosophy
The Raku tea bowls, as pioneered by Chojiro, used monochrome black or red glazes—in marked contrast to the brightness of the San cai wares from which they evolved.[4] His work reflected a unique aesthetic which emphasizes simplicity and aims to eliminate movement, decoration, and variation of form. His Raku wares symbolize more directly than any other kind of ceramic the ideals of wabicha, ("cha" meaning "tea") the form of the tea ceremony based on the aesthetics of wabi advocated by Sen no Rikyu. [5]
Raku wares are hand-formed rather than thrown on the wheel, which makes them very different from other kinds of Japanese ceramics. Hand-forming allows the spirit of the artist to speak through the finished work with particular directness and intimacy. Chojiro, however, through his negation of movement, decoration and variation of form, went beyond the boundaries of individualistic expression and elevated the tea bowl into a manifestation of abstract spirituality.[6]
His works aim at "monochromatic silence," as if creativity tries to go beyond the act of creation itself, a paradoxical and extraordinary spiritual effort.
Lineage of the Raku House
Fifteen generations of Raku family members have directed the Raku potteries until today. Tanaka Sokei, 1534?-1594, directed the Raku workshop together with Chojiro and the grandfather of Chojiro's wife. He became the master potter after the death of Chojiro. Jokei II, Sokei's son was adopted by Chojiro, inheriting the Raku name and pottery.
Jokei introduced a white glaze and more movement to the pottery shape. His son, Donyu III, 1599-1656, is considered the most skillful Raku potter. Ichinyu IV, 1640-1696, the eldest son of Donyu, was only 17 when his father died. His style is closer to that of Chojiro than to the more innovative and decorative style of Donyu. He invented the shuyaku glaze, the black glaze mottled with the red, which made a significant influence on the work of successive generations.
Sonyu V, 1664-1716, was born as a son of Kariganeya Sanuemon, the head of a great artistic family, and was later adopted by Ichinyu to carry on the Raku name and works. Sanyu VI, 1685-1739, was born as a son of Yamatoya Kahei and later taken into the Raku family as Sonyu's son-in-law. Chonyu VII (1714-1770) was the eldest son of Sonyu; his tea bowls are uniformly large and modest. His son, Tokunyu VIII 1745-1774, followed him; and then Chonyu's second son, Ryonyu IX 1756-1834; and Ryonyu's son, Tannyu X 1795-1854 followed. Keinyu XI 1817-1902, was adopted as Tannyu's son-in-law; and then his eldest son, Konyu XII 1857-1932, became director. He was confronted with difficulties together with his father when he succeeded to the house, since the tea ceremony's popularity was still in decline since the dawn of the modernization of the Meiji period, begun in 1868.
He was followed by Seinyu XIII 1887-1944, the eldest son of Konyu, succeeded as the thirteenth generation in 1919. Seinyu's 57 years were certainly not the happiest, with the outbreak of two successive World Wars. He principally followed the traditional style of Raku tea bowls, reflecting his serious personality. He was an enthusiastic researcher on glazes, applying various minerals from different sources in Japan for experimentation. Studying at the Tokyo School of Art helped him to establish a unique style of his own, clearly distinguished from those of the past generations. His trimming of the bowls is more precisely applied for the purpose of giving structural power to the composition of tea bowls.
Kichizaemon XV, born in 1949, assumed leadership of the in 1981. He is the current head of the Raku House, and the fifteenth in line of leadership. After graduating from the Sculptural Department of the Tokyo University of Fine Arts in 1973, he went to Italy for further studies. [7]The Raku house and its workshop are still located on the west side of the former Imperial Palace in Kyoto, maintaining a traditional Kyoto style architectural design. A museum at the site holds many of the historical Raku bowls.
Japanese Tea Ceremony
The role of the Raku bowl is tied profoundly to the success of the tea ceremony. Japanese "Cha-no-yu" (“hot-water tea”), a time-honored institution in Japan, is rooted in the principle of Zen Buddhism and founded upon the adoration of the beautiful in the daily routine of life. It is an aesthetic way of entertaining guests, in which everything is done according to an established order. Without the proper Raku tea bowl and utensils there can be no tea ceremony. The nature of the bowl, dependent on the artisan, determines the success or failure of the tea ceremony. [8]
The strict practices of the Japanese Tea ceremony required careful selection of the bowls and instruments each year to reflect the spiritual practice of the tea master. The choosing of the year's bowl gave prestige to the family of potters that created it and could bring fame or disgrace to the potters who vied for the honor of the acceptance by the tea master. Each bowl chosen was given a name, by the tea master, that reflected the character held within the bowl. Only the greatest tea master could receive the Emperor and other dignitaries, to his tea ceremony, which afforded the master great honor and increased his reputation, as well as that of Raku pottery used in his ceremony. The bowls themselves could sometimes make or break the prestige of the master. Pottery houses would destroy any inferior bowls to protect their name.
Only in modern times have women been allowed to perform the Cha-no-yu.
Western Raku techniques
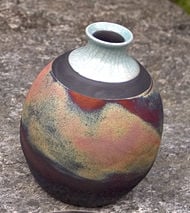
Raku in the west is popular because the results offer a myriad of unique iridescent glazes, crackling, and black-soot dyed surfaces. Raku pottery can be placed into a warm kiln, unlike other types of ceramics, and the kilns need not be large, as in stoneware firing. The challenge is to take a pot out of a very red hot kiln—usually with heavy gloves, a safety mask, and tongs—and then place it into a receptacle for burning without breaking the pot. Very large pieces are especially difficult to lift out of the kiln.
A lid must be placed on the receptacle quickly, since the organic materials burst into flame, causing rapid oxygen reduction, which intentionally stains the body of the pot black with soot. The pot will then be scrubbed after cooling to remove excess soot and reveal what the "magic" of the Raku technique produces. Unpredictable results often disappoint the potter, but the fast firing time encourages potters to "try it again."
Western Raku is typically made from a stoneware clay body,[9] and glaze-fired (the final firing) between 1450-1800°F. The process is known for its unpredictability, particularly when reduction is forced, and pieces may crack or even explode due to thermal shock. Pots may be returned to the kiln to re-oxidize, although each successive firing has a high chance of weakening the overall structural integrity of the pot.
The use of a reduction chamber at the end of the Raku firing was introduced by the American potter Paul Soldner in the 1960s, in order to compensate for the difference in atmosphere between wood-fired Japanese Raku kilns and gas-fired American kilns. Typically, pieces are placed in masses of combustible material (e.g., straw, sawdust, or newspaper) in order to provide a reducing atmosphere for the glaze.
The glaze firing times for Raku ware are short, an hour or two as opposed to up to 16 hours for high-temperature stoneware firings. This is due to several factors: Raku glazes mature at a much lower temperature (under 1800°F, as opposed to almost 2300°F for high-fire stoneware); kiln temperatures can be raised rapidly; and the kiln is loaded and unloaded while hot and can thus be kept hot between firings.
Because temperature changes are rapid during the Raku process, the clay bodies used for Raku ware must be able to cope with significant thermal stress. The usual way of dealing with this is to incorporate a high percentage of quartz, Grog (pre-fired clay that has been finely ground), or Kyanite into the body before the pot is formed. Each of these materials is used to add strength to the clay body and reduce thermal expansion. When used for over 10 percent of the clay body, quartz can cause glaze defects known as dunting or shivering. Therefore, Kyanite is often the preferred material because it contributes both mechanical strength and significantly reduces thermal expansion. Although any clay body can be used, most porcelains and white stoneware clay bodies are unsuitable for the Western Raku process unless some material is added to deal with thermal shock which would alter the fine texture of porcelain.
Western Raku potters rarely use lead as a glaze ingredient, due to its toxicity. (Japanese potters now also have become to avoid lead in the glazes.) Although almost any low-fire glaze can be used, potters often use specially formulated glaze recipes that "crackle" or "craze" (present a cracked appearance), emphasized by the black soot stain of the Raku process.
Contemporary Raku potters
Many Western potters studied in Japan to inherit the ancient style of Raku pottery. One of these was Bernard Leach (1887–1979) who established the Leach Pottery in Saint Ives, Cornwall, in 1920. Leach spent many of his early years in the Far East and learned the art of Raku in Japan.
American Raku artist Michele Rudenko of northern California states concerning the illusive results of Raku work: “While I can and do plan for a particular outcome, the very nature of Raku often creates a result that is surprisingly different from the original vision; this results in the singular power of each piece. Raku is a marvelous lesson in non-attachment that guides me through a deeper understanding of the process, abundant possibility and of course, myself.” [10]
Another American Raku potter is Gary R. Ferguson, from Nampa, Idaho, who produces a variety of Raku ware, including beads, and offers his glaze recipes to others. Nina Fernstrom-Duong produces colorful hanging Raku fish ornaments; and Audrey Skeen uses natural materials, such as horse hair, added to her pottery designs.
See also
- Tea ceremony
- Sen no Rikyu
- Kiln
- Pottery
- Stoneware
- Earthenware
- Porcelain
- Clay
- Korean pottery and porcelain
- Glaze
Notes
- ↑ Styles of Raku. www.e-yakimono.net. Retrieved August 21, 2007.
- ↑ History of Raku Ware. www.raku-yaki.or.jp. Retrieved August 19, 2007.
- ↑ Styles of Raku. www.e-yakimono.net. Retrieved August 21, 2007.
- ↑ At that time three-colored glazed San cai ware, based on technology from the Fujian region of China was produced in and around Kyoto. Chojiro was presumably familiar with such techniques. A written record confirms that Ameya, Chojiro's father, originally from China, is thought to have been the one who introduced the techniques of three-colored glazed pottery from China, although none of his works has survived to prove this. History of Raku Ware. www.raku-yaki.or.jp. Retrieved August 21, 2007.
- ↑ Central to the philosophy of wabicha were notions of "nothingness" deriving from Zen Buddhism and the "isness" of Taoism.
- ↑ Raku Museum of Japan History of Raku Ware. www.raku-yaki.or.jp. Retrieved August 21, 2007.
- ↑ History of Raku Ware. www.raku-yaki.or.jp. Retrieved August 19, 2007.
- ↑ Tea Ceremony. www.britannica.com. Retrieved August 19, 2007.
- ↑ This is unlike the early Japanese Raku, which used earthenware fired at a lower temperature.
- ↑ EartHeart Studios Art of Raku. artofraku.com. Retrieved August 21, 2007.
ReferencesISBN links support NWE through referral fees
- Hamer, Frank and Janet. The Potter's Dictionary of Materials and Techniques. A & C Black Publishers, Limited, 1991. ISBN 0812231120
- Peterson, Susan. The Craft and Art of Clay. The Overlook Press, 1996. ISBN 0879516348
- Pitelka, Morgan. Handmade Culture: Raku Potters, Patrons, and Tea Practitioners in Japan. University of Hawaii Press, 2005. ISBN 0824829700
External links
All links retrieved December 7, 2022.
- Raku museum Kyoto. www.raku-yaki.or.jp.
- Japanese Pottery Information Center. www.e-yakimono.net.
- Raku Glaze Recipes. www.garyrferguson.com.
Credits
New World Encyclopedia writers and editors rewrote and completed the Wikipedia article in accordance with New World Encyclopedia standards. This article abides by terms of the Creative Commons CC-by-sa 3.0 License (CC-by-sa), which may be used and disseminated with proper attribution. Credit is due under the terms of this license that can reference both the New World Encyclopedia contributors and the selfless volunteer contributors of the Wikimedia Foundation. To cite this article click here for a list of acceptable citing formats.The history of earlier contributions by wikipedians is accessible to researchers here:
The history of this article since it was imported to New World Encyclopedia:
Note: Some restrictions may apply to use of individual images which are separately licensed.